How Forestry Companies Can Supercharge Their Manufacturing Execution System (MES)
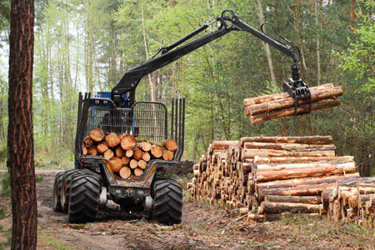
As the demand for construction materials and other wood-based products continues to grow, forestry companies have a big opportunity to boost their bottom lines. From harvesting trees to the final products coming out of sawmills, significant operational improvements are available to those who invest in the appropriate technology.
However, it is typical for many in the industry to rely solely on the manufacturing execution system (MES) supplied by their equipment manufacturers to track operations and performance.
Even though wood production appears to be continuous, there is often a waiting period between parts of the process. Each area essentially functions as a unit unto itself, where important specifications must be met before the next step can take place. With more efficient data consumption, mills can generate vastly improved outcomes.
Adding a real-time data management platform, such as the PI System, allows forestry companies to unleash the power of the data generated by an MES.
Going Beyond Traditional Tracking
When it comes to managing costs by tracking raw material and overhead, the MES will perform as expected. It knows when a batch of logs arrived and how it became a batch of plywood three days later, including the product ID and which personnel were running the machines in stages along the way. For traceability, the MES serves its purpose.
However, an MES doesn’t account for other operational conditions that occur over time. Since it doesn’t track equipment performance and in-process quality in between the stages, layering the PI System over the MES adds another level of context to the data. Engineers and operators can use this new capability to react to potential problems, or problems they’ve already identified, and thereby make improvements throughout the process.
The additional insight contributes to predictive and prescriptive maintenance of equipment; optimized energy consumption; improved safety, such as dust extraction; and less variability in materials. Being able to determine the contributors to variability in output and having the ability to keep the variability of raw material within a set range, for instance, can significantly reduce waste and increase productivity.
One company making plywood used the PI System for tracking the steaming process that follows debarking. Logs need to be removed from the steamers within a limited time range to avoid quality problems in the next step of the process. With the PI System, alerts were established to prompt operators to remove the logs in a timely fashion. The result was a significant improvement in quality and consistency. Next, the company plans to expand into advanced analytics to reduce the variability of the raw material, which would boost throughput.
In addition to the steaming process, the PI System is used in the clipping, drying, adhesive application, continuous press, and packing parts of the plywood operation. By taking a step further into even more complex analytics, it is possible for companies to optimize production around the demand that is coming into the system by analyzing market data in conjunction with their own operational information.
For example, one PI System customer is crunching this combination of data — specifically its capacity to produce certain products and shifting demand — to better assess when to switch from making one product line to another. This is beginning to help the customer adapt to a large and dramatically shifting demand for building materials.
Where To Start
Any digitalization effort without a clear objective and a methodical plan will likely fail, but getting it right can be an overwhelming task. The best strategy for implementing a digital transformation initiative, such as using the PI System in conjunction with an MES, is to start with an assessment to determine which area of opportunity will have the largest impact on the bottom line at the facility.
Next, add analytics to the data being captured in that area, to provide context, then rank the issues in order of impact. Once an order is set, tackle the biggest issue by categorizing the different events that contribute to it.
A common investment strategy in digitalization is thinking big but starting small. Minimize costs for a real-time data infrastructure by putting a system together one piece at a time. In many cases, a subscription model can heavily reduce the barriers of entry to the technology. Begin by targeting the most important use case, one part of the process, invest in a solution, demonstrate value, then use the “proceeds” from that project to invest in the next piece until a fully functional integrated system is in place. Along with the ROI benefits, the company will also build its internal skills necessary to continue moving forward faster toward the goal of operational excellence.